Nissan Invests in Quality with Yxlon Computed Tomography System
With talk revolving around the demise of manufacturing in Australia and the shrinking automotive component manufacturing activity, one Original Equipment Manufacturer (OEM) defies the trend. Nissan Australia, a fully integrated OEM has been increasing its manufacturing capabilities and will be the only car manufacturer with a direct presence in Australia after 2016 with Ford and Holden shutting down local manufacturing. With projected growth into the future, Nissan are investing in equipment to ensure they maintain their technological and quality advantages.
Nissan operates an aluminium casting facility in Australia (Nissan Casting Australia). They have a 90,000 square metre plant that houses both high and low pressure die casting machines with capacity to produce 10,000 tons of cast parts and accessories per year. From this, over 2 million parts with a value of in excess of $65 million are exported to other Nissan assembly operations around the world including Japan, the US, Thailand, South Korea and Mexico, as well as other manufacturers such as Calsonic Kansei and Jatco, a Japanese transmission manufacturer.
For the last 6 months, the Nissan Casting plant has been operating three shifts a day, 7 days a week to keep up with demand. With demand set to grow with new contracts having been awarded to NCA, they are also recruiting more staff, dispelling the myths about Australian manufacturing.
When asked why business was booming for NCA, Managing Director, Peter Jones replied, our success is not based solely on price. We can proudly say that the demand for our products is based on quality. If you look at the finish, accuracy and tolerances of some of the parts we manufacture, like those for the Nissan LEAF and e-NV200 electric vehicles, you might think they have been machined when in fact they are straight out of the mould. Such is the quality of these castings, that we have the exclusive contract to supply these parts.
With quality being such an important factor in the future success and sustainability of NCA, they have recently invested around $500,000 in a new Y.MU2000 Computed Tomography (CT) system from Yxlon (Germany). This is the technology that Formula 1 teams use to ensure their parts meet specifications. The system works in the same way a medical CT scanner works and allows operators to delve non-destructively into the inner structure of a casting by generating a 3-dimensional reconstruction. This will allow them to see if porosity and/or casting defects are present, check tolerances and make adjustments accordingly to correct any problems, thus maintaining quality.
The data generated will have benefits for quality control as they will be able to monitor casting quality. Additionally, there is the benefit for new products where the use of CT can be applied to the optimisation of tooling and systems. This is of particular importance with castings becoming more complex and thinner walled to save on weight and materials, and ultimately cost.
Richard Trett, Managing Director of AXT, Yxlons Australian distributor said, this is the second supplier we have worked with this year who is looking to leverage their unique technical expertise. Investing in quality, rather than price is the way to ensure the future of Australian manufacturing.
Some of the parts that NCA manufacture include oil pans, gearbox housings and final drive housings that go into more than 30 different models from the Nissan, Infiniti and Renault stables. This includes the all-new, soon-to-be-released Nissan NP300 Navara.
With continued investment in technology, the future for this auto manufacturer in Australia seems assured. It also demonstrates that quality can often win the battle over price and this should be a platform for Australian manufacturing to build from.
Posted May 27, 2015
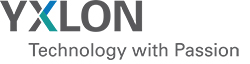